Parquet laying
Parquet laying
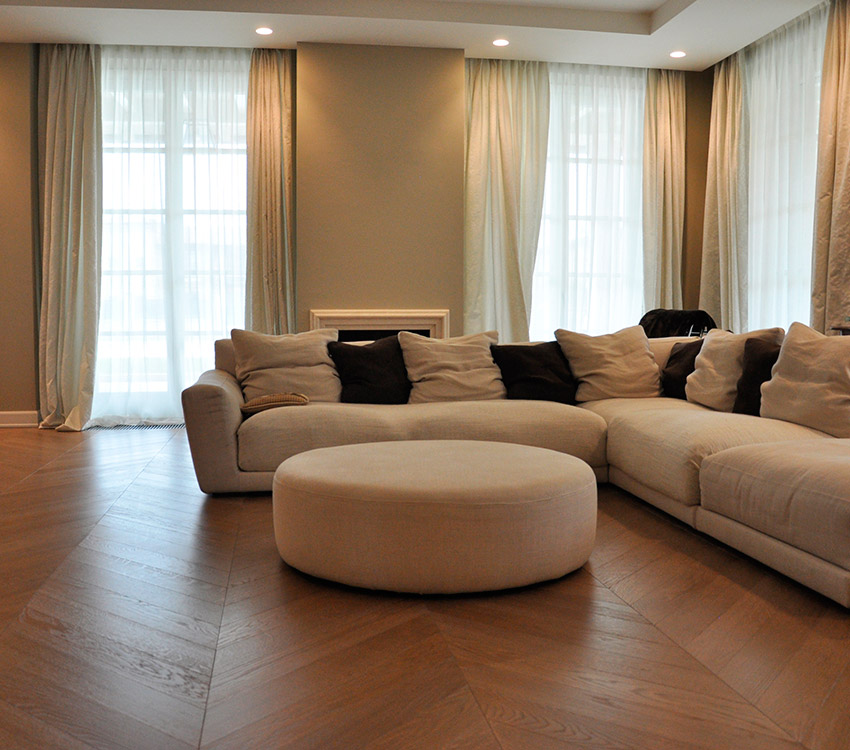
Installation options
Once the essence, the finish and the structure of the parquet have been chosen, what remains to be evaluated is the so-called the laying geometry, i.e. the design to be obtained by laying the boards together, and the technique of setting up the parquet itself.
After carefully evaluating these factors with the help of a installer, the parquet can be laid in different ways.
After carefully evaluating these factors with the help of a installer, the parquet can be laid in different ways.
Floating laying
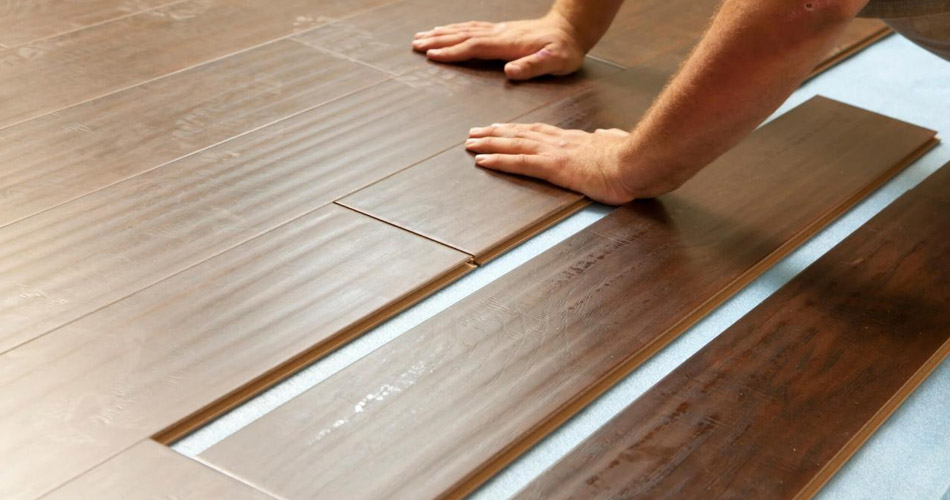
Floating laying is the most environmentally friendly method of laying wooden floors because the use of vinyl glue is very limited. This type of installation is the optimal solution for the installation of our 3-layer parquet which, thanks to its particular construction, guarantees excellent stability over time.
It consists in placing the elements of the parquet upon the laying surface without having to glue the lower part of the boards; the installer will join the planks together with the male / female joint using vinyl glue free from formaldehyde and other harmful substances.
For a perfect installation, between the cement screed and the wooden floor, a polyethylene sheet can be interposed with a vapor barrier effect and a sound-absorbing cork sheet to further improve the acoustic reduction of footsteps and other noises.
It consists in placing the elements of the parquet upon the laying surface without having to glue the lower part of the boards; the installer will join the planks together with the male / female joint using vinyl glue free from formaldehyde and other harmful substances.
For a perfect installation, between the cement screed and the wooden floor, a polyethylene sheet can be interposed with a vapor barrier effect and a sound-absorbing cork sheet to further improve the acoustic reduction of footsteps and other noises.
Installation with glue
The glued laying is done by spreading the glue on the surface of the screed with a spatula suitable for this process, distributing the glue evenly without creating air bubbles between the screed and the wooden floor. With wide semi-circular movements, quite usual for professional installers, very close and evenly distributed glue lines are created, which guarantee good adhesive contact between the wooden floor and the underlying screed.
It is important to dose the optimum amount of glue for good gluing and to use glues that are free from percentages of water that could deform the wooden floor boards.
The use of an environmentally friendly glue, free from harmful substances, can determine the conditions for complete recycling of the material used at the end of its life.
It is important to dose the optimum amount of glue for good gluing and to use glues that are free from percentages of water that could deform the wooden floor boards.
The use of an environmentally friendly glue, free from harmful substances, can determine the conditions for complete recycling of the material used at the end of its life.
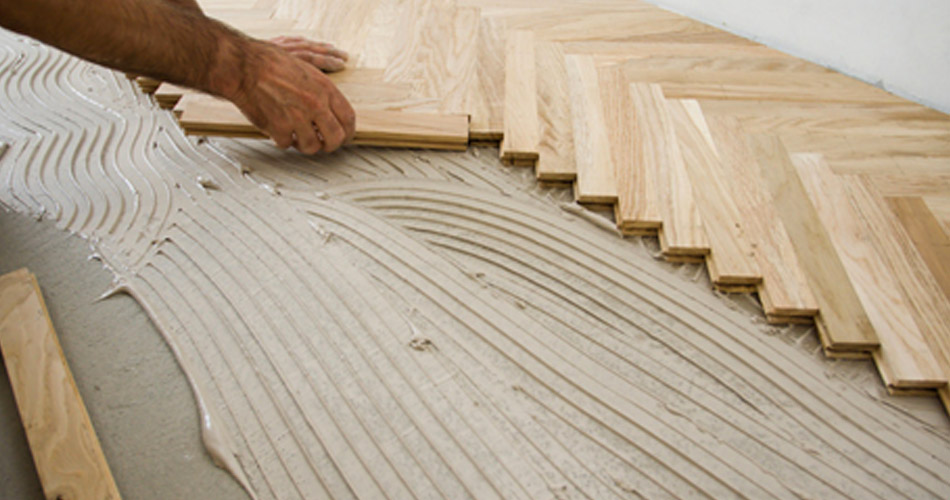
Installation on a heating screed
It is advisable to glue the floor boards onto a heating screed using glues free of percentages of water that could deform the wooden floor boards. It is important to put the heating system into operation at least 3 weeks before laying in order to stabilize the screed. During this period of time the system must be brought to a steady state gradually increasing the temperature by about 5° C per day until the maximum allowed temperature of 30° C is reached.
This temperature must be maintained for about 2 weeks in order to release the residual moisture from the screed. The plant must then be turned off gradually within 5 days before laying to allow the screed to stabilize. In this phase it is important to keep the rooms ventilated to favour the exit of the humidity that will form during the heating and cooling cycles of the screed.
Before laying, the humidity of the screed must be checked with a carbide hygrometer.
This temperature must be maintained for about 2 weeks in order to release the residual moisture from the screed. The plant must then be turned off gradually within 5 days before laying to allow the screed to stabilize. In this phase it is important to keep the rooms ventilated to favour the exit of the humidity that will form during the heating and cooling cycles of the screed.
Before laying, the humidity of the screed must be checked with a carbide hygrometer.
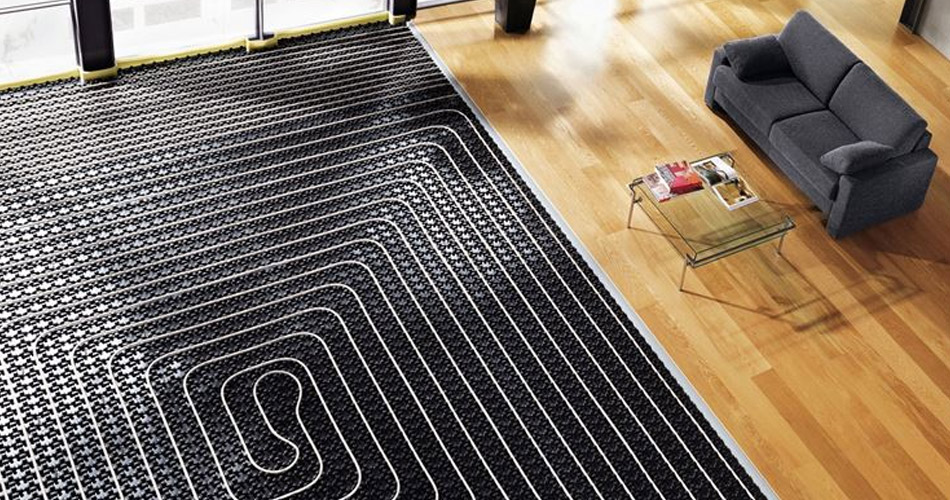
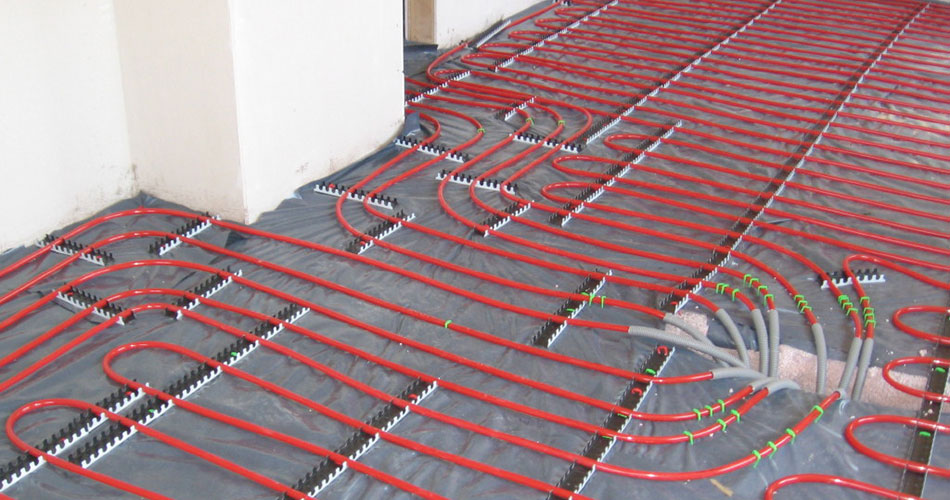