Our production
All our products, catalogue or custom made products, wooden floors, wall claddings or accessories, are made in our factory in Cecchini di Pasiano, in the province of Pordenone. It is a 100% made in Italy production that begins from the selection of the raw materials, where trunks of the various wood species are checked and chosen for size and quality to be subsequently cut in veneers that will then be dried according to precise parameters.
The production process continues inside our premises with the preparation of the supports: the inner core and the counter-balance of boards, then with the gluing phase for the creation of a 2-layer or 3-layer structure.
Once the boards have been glued and pressed, they are left to rest for a period. The unfinished boards are then ready for the following manual processes and finishing phases. Knots are cleaned and filled with putty, where necessary, then the planks are treated on their surface: from simple sanding or brushing to planing by hand, to finishing with a gouge or other required work.
We make the male & female milling on all four sides of the board, with a slight bevel.
Now the material is ready for the oiling phase, using only natural oils, free from formaldehyde and other toxic substances. The finishing oils are applied repeatedly and left to dry naturally in special racks without using ovens, lamps or other machinery.
The production process ends with the final quality control, where we carry out an overall check of the product with extreme care. Only after having successfully passed final quality control the product is allowed to move on to the packaging area where our floors are prepared for shipment and final delivery to the customer.
The production process continues inside our premises with the preparation of the supports: the inner core and the counter-balance of boards, then with the gluing phase for the creation of a 2-layer or 3-layer structure.
Once the boards have been glued and pressed, they are left to rest for a period. The unfinished boards are then ready for the following manual processes and finishing phases. Knots are cleaned and filled with putty, where necessary, then the planks are treated on their surface: from simple sanding or brushing to planing by hand, to finishing with a gouge or other required work.
We make the male & female milling on all four sides of the board, with a slight bevel.
Now the material is ready for the oiling phase, using only natural oils, free from formaldehyde and other toxic substances. The finishing oils are applied repeatedly and left to dry naturally in special racks without using ovens, lamps or other machinery.
The production process ends with the final quality control, where we carry out an overall check of the product with extreme care. Only after having successfully passed final quality control the product is allowed to move on to the packaging area where our floors are prepared for shipment and final delivery to the customer.
First cut of the trunk
The first cut of the trunk takes place only after an accurate selection based on quality and size.
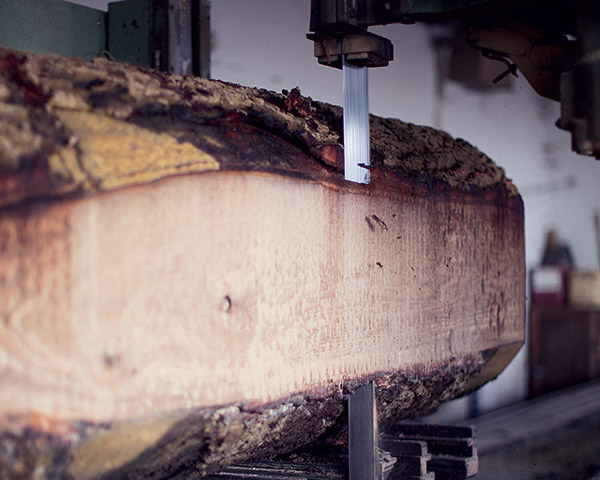
Cutting and spreading the plank for a first natural seasoning in the air
The planks, once cut, are naturally seasoned in the open air before being placed in a drying chamber.
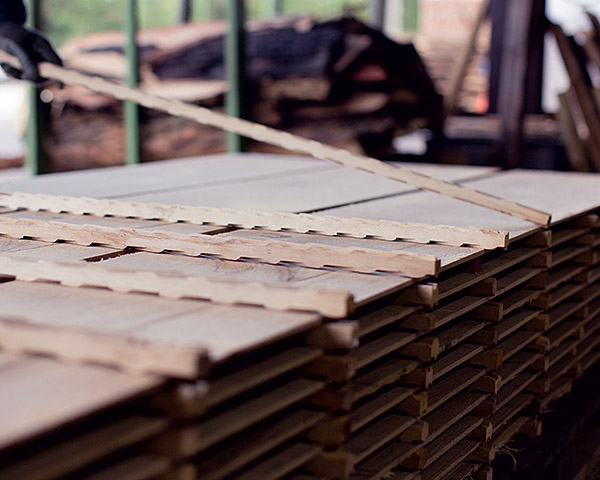
Drying of the planks in traditional dryers
After seasoning, the planks are dried in special traditional dryers.
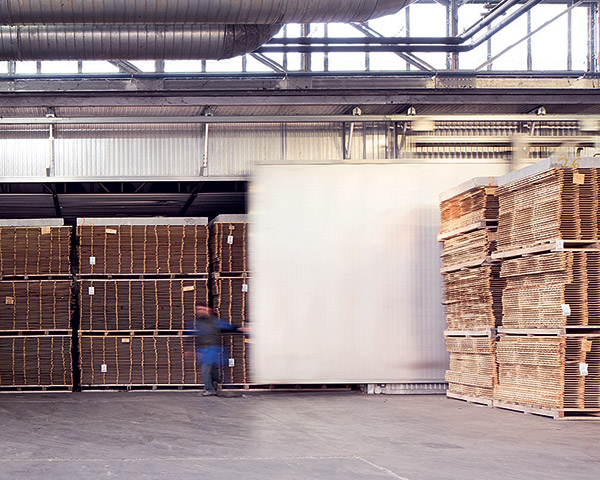
Trimming, calibration and selection of planks
In this phase the planks are appropriately selected and divided according to the type chosen, calibrated and trimmed.
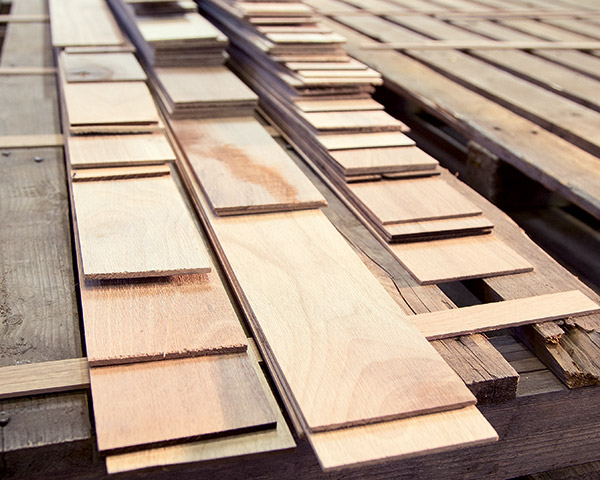
Glueing
For the glueing we use a vynle glue free from formaldehyde and other harmful substances, which is resistant to water and moisture.
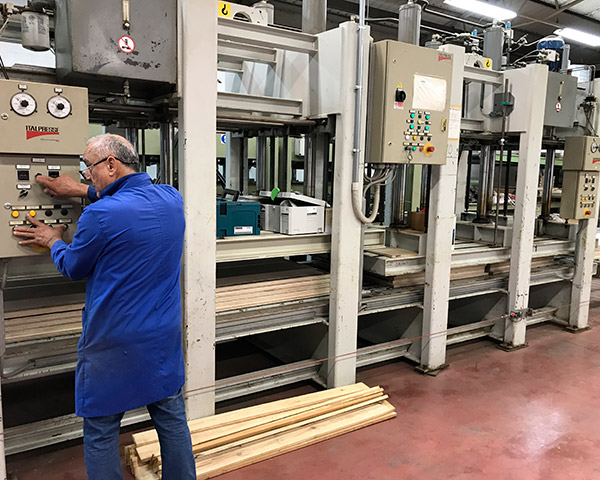
Cleaning of knots and grouting
The knots in the wood, especially present in the rustic choice and karachter, are manually cleaned with care and then stuccoed.
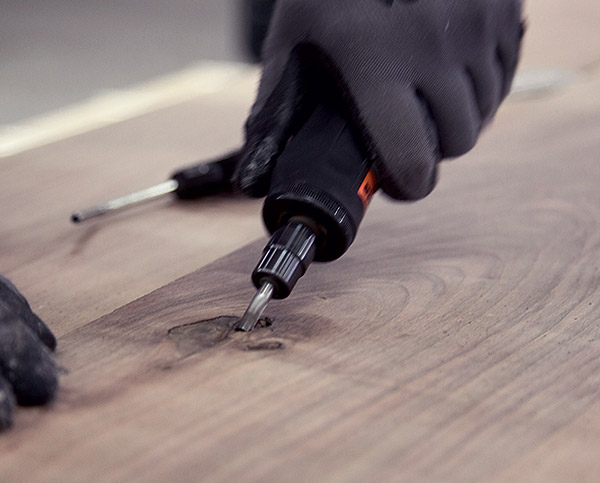
Handmade craftsmanship
By using ancient and traditional tools our expert craftsmen can do some work by hand on the boards, such as: planing, gouging, excavation of knots and deconstruction.
Profiling
On each table the male/female profiling is carried out on all 4 sides with a slight bevel.
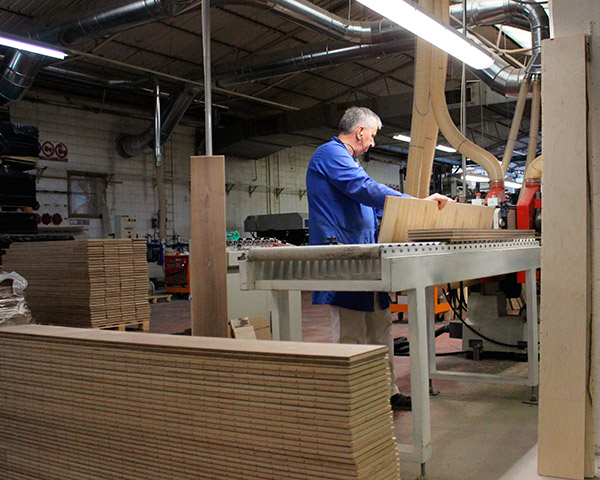
Finishing
We do the finishing in a traditional way, several times according to ancient traditions and using natural oils. The following drying phase is carried out in a completely natural way, simply by air drying, according to controlled temperature and humidity parameters. Kilns and/or other machines are not used.
Packaging
At the end of the production process, after having successfully passed the final quality control, the boards are packed in special cardboard packs with the Lignum Venetia logo, in order to protect them from possible shocks during transport. The complete pallet is then well closed using nylon, protective straps and corners.
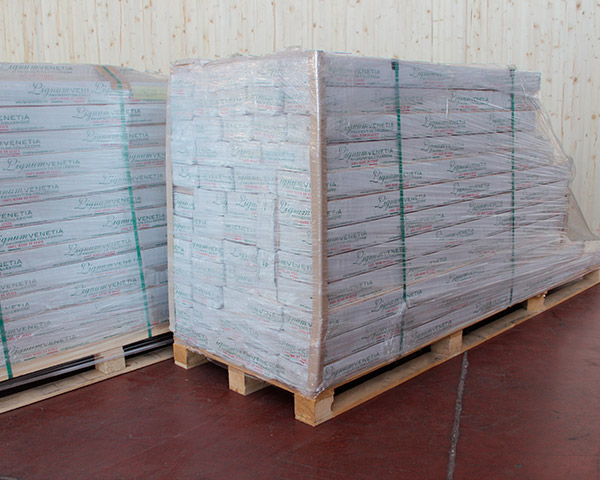